Blog Archive
-
▼
2011
(14)
-
▼
September
(9)
- Understanding and using protective hoods
- Check your PPE Between Calls
- Balancing Breathability with Protection in Turnouts
- Determining When PPE Needs To Be Retired
- Attorney: Fire Departments Need to Develop Social-...
- How moisture impacts thermal insulation in PPE
- The Future of PPE
- Doffing Superheated Gear
- DRD Care, Inspection and Installation
-
▼
September
(9)
Real Kings of Logistics
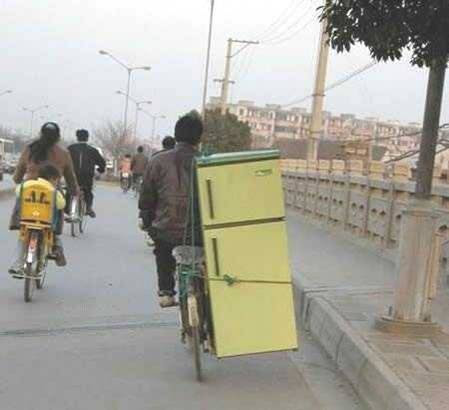
Sunday, September 18, 2011
DRD Care, Inspection and Installation
The linked video from Globe shows how to clean, inspect and install the drag rescue device (DRD) in your turnout coat.
Additional Information
In-station cleaning of PPE should be restricted to small soiled areas. General cleaning should be done by sending the garment out to our cleaning/inspection vendor.
If you find damage to the DRD or any other part of your PPE, report the damage to the Quartermaster.
Doffing Superheated Gear
Raise arms to dissipate heat
Open coat.
Have someone remove the coat by rolling it away from the body.
Do not:
Wet down gear while being worn.
Compress the gear against the body.
The Future of PPE
(Click the title to go to the article)
The author looks back on the past year of PPE design and standards-making. He is asking for firefighters to continue to ask "what if." If you present a what if then with the cooperation of the manufacturers you can make PPE lighter, safer, and more effective. You need to participate.
How moisture impacts thermal insulation in PPE
with Jeffrey O. and Grace G. Stull
Sponsored by Globe
Last month, we wrote about the different ways that firefighter clothing gets wet. While expected, this is significant because water or moisture in clothing can have a variety of effects on its performance.
The most obvious concern is the impact of moisture on clothing thermal insulation, but water can be a factor for other kinds of performance. For example, clothing that retains too much moisture from exterior sources can become heavier and result in greater stress to the wearer.
Moreover, wetness in gloves can affect dexterity and grip. Materials that easily pick up water may also more easily retain various hazardous contaminants. Understanding how moisture affects your clothing allows you to better judge your circumstances and realize conditions when your protection may or may not be compromised.
There are also a number of overly broad generalizations that have come about in the industry, some of which are simply not true and can result in poorer understanding of clothing protection. Several years ago, we worked with a large metropolitan fire department that had just started wearing hoods over the previous few years and the firefighters in that department had little experience with the ways that hood materials attenuated the levels of heat. One of the early concerns that arose was the wearing of wet hoods. The opinion spread throughout the department was that it was dangerous and therefore many firefighters opted to go without a hood rather than wear a wet hood.
In response to these concerns, we conducted a study for the department along with some other industry experts and measured insulation levels for hoods with the varying levels of moisture that could be expected (dry, damp, and saturated).
Different tests
The hoods or hood materials were subjected to an array of different heat exposure tests ranging from the extreme (simulated flashover) to the more ordinary (low levels of radiant heat). For small scale tests, the predicted time to second degree burn injury was measured along with the time to pain.
The difference in these two measurements is known as the alarm time, which is the amount of time that the average individual would first feel pain to the time for the onset of burn injury. Full scale tests were also performed with a manikin instrumented with sensors in different locations that would predict what parts of the body would sustain burn injury during a simulated fireground flashover.
The results of this study showed some fairly remarkable findings. At the lowest level of radiant exposure, dry hoods outperformed damp hoods, but saturated hoods provided more protection than damp hoods. At a moderate level of radiant heat exposure, dry, damp, and saturated hoods had equivalent protection. At higher levels of radiant heat, the saturated hoods showed slight advantages over damp and then dry hoods.
These differences became more distinct as the radiant level increased; however, the overall relative protection diminished as compared to lower levels of radiant exposure. Lastly, the instrumented manikin results provided similar results for a flashover as the high radiant heat level tests — all areas of the face, neck, and ears were burned with no hood.
There was a substantial reduction in burn areas for dry hoods, but additional decreases were observed for increasing levels of moisture. Yet, the most definitive result was that in no cases was the wearing of no hood more protective with wearing a hood under any moisture condition.
Of course, the hoods that were tested in the study described above were of relatively simply construction — two plies of a homogeneous knit material. Moisture effects on thermal insulation grow increasingly complicated with multi-layer garments having different types of materials used in their construction.
Variable conditions
In fact, several studies have been performed in the past to measure various forms of heat transfer through materials under different wetting conditions. Many of the early studies focused on differences between impermeable and permeable moisture barriers.
For example, one study done nearly 30 years ago demonstrated that the thermal protective performance of firefighter clothing composites (outer shell, moisture barrier, and thermal barrier) changed radically depending whether the moisture was in the shell, the liner (combination of moisture barrier and thermal barrier) or both.
This testing further showed in some cases, such as the lining being wet while the shell was dry, that alarm time was lowest and that permeable moisture barriers provided substantially more warning to the firefighter before the onset of a burn.
Related testing showed varying the amount of the water generally favored impermeable barriers over permeable barriers. Testing performed in separate studies 12 to 15 years later showed many of the same trends, but refined the results. To say the least, this test information simply demonstrated how complicated moisture effects could be on insulation.
More recent tests have examined the effects of stored energy in clothing over a relatively long exposure to low levels of radiant heat that is then followed by rapid compression of the clothing layers against the skin. In this testing, the worst condition has been found when impermeable materials are placed over breathable materials for certain levels of moisture in the liner only.
That is not to say any firm conclusion can be drawn by these findings, rather, a specific case has been identified where firefighters might be at greater risk for unexpected burn injury. Testing has also shown that this potential can be mitigated by other factors. All tests are nothing but snapshots of some very specific conditions, some of them realistic, others not and it is generally difficult to draw a broad conclusion from just one set of testing for relating moisture effects in clothing.
What you must remember
To understand moisture effects on clothing, it is important to remember that the moisture in clothing both absorbs and conducts heat. In absorbing heat, the water provides additional mass in the material. However, as the moisture is heated, it can reach scalding temperatures if the heat is not dissipated through the clothing or by other means.
This is why the source of moisture and where it is located becomes very important in determining possible effects of moisture on thermal insulation. Water temperatures on the exterior of the clothing will rise very rapidly because the moisture is closer to the source of heat. Yet at the same time, this moisture has a freer path for evaporation off the surface or wicking into other parts of the clothing.
Additional contact directly with liquids or with wet surfaces can serve to replenish the moisture. In contrast, moisture generated primarily from sweating within the clothing interior can also travel but remains within a closed environment. Furthermore, the interior clothing layers may be next to the skin.
But unlike the laboratory experiments, moisture in the material is replenished through additional sweating. This accumulation of moisture will or will not become a problem in terms of thermal insulation depending on the level and length of heat exposure combined with the moisture management qualities of the clothing.
Main problems
Generally, the largest problems occur when there are radical changes — changes in the exposure conditions or changes in way the clothing fits on the individual. If the fire scene worsens with a rapid build up of intense heat, clothing insulation can be overwhelmed and the position of the moisture in the clothing can play a dramatic role in affecting the propensity for increased heat transfer and storage of thermal energy.
Likewise, if clothing tightens against the skin or underclothing from compression or movement, new pathways for heat transfer are created. This is one of the reasons why many manufacturers caution firefighters to regularly change their position to minimize heat transfer to one area of their body. Still, some material systems will retain heat. If in combination, these materials do not facilitate moisture spreading throughout the garment, then under some conditions burn injuries can occur with little or no warning.
It would be nice if there was a simple answer for recognizing what levels of moisture, together with where that moisture is located, the condition of the garment, and heat exposure levels could allow prediction of burn injury. That approach is extremely unlikely as exposure conditions vary dramatically as do the factors which affect moisture in clothing and its subsequent impact on thermal insulation.
For the time being, the best advice is to realize that moisture can impact your garment's thermal insulation and be alert to potential signs that long exposures followed by rapid changes in your environment can lead to increased variability in your protection. While this principle applies to garments, it equally applies to other parts of the ensemble, especially gloves and hoods.
Sponsored by Globe
Jeffrey O. and Grace G. Stull are president and vice president respectively of International Personnel Protection, Inc., which provides expertise on the design, evaluation, selection and use of personnel protective clothing, equipment and related products to end users and manufacturers. They are considered amongst the leading experts in the field of personal protective equipment. Send questions or feedback to Jeff or Grace at Jeffrey.O.Stull@FireRescue1.com. The views of the author do not necessarily reflect those of the sponsor.
from ppe101.com
Attorney: Fire Departments Need to Develop Social-, Digital-Media Policies
This article discusses the need for departments to have policies that address the use of social media sites and digital images.
The author strongly urges departments to establish policies that address social media and digital images, if they don’t already exist. Here are a few tips he shared for creating such policies:
Policy statements should make clear that all images taken by on-duty personnel are the property of the department.
Authorized photographers should be identified by the chief and use only department-issued cameras. Only authorized photographers should take images at an incident.
Images should be inventoried and archived in a secure location on the department’s server.
Once they’re archived, they should be deleted from the camera. This should be done as soon as feasible — ideally, as soon as the crew returns to the station, but at least by the end of the shift.
The use of titles, department logos, department-owned images, or identification as a member of the department that creates an impression that the member is a spokesperson for the department should be prohibited.
Any social-media policy should address digital images — even if the department has a digital media policy in place.
Determining When PPE Needs To Be Retired
|
Determining when PPE needs to be retired
By Jeffrey O. and Grace G. Stull
Probably one of the most difficult tasks when it comes to judging PPE is to determine when clothing should be retired. Sure, there are many cases when the decision is quite clear that clothing must be disposed of — garments that have been charred and embrittled through extreme heat exposures, garments grossly contaminated with tar, paint, or other substances, or garments exhibiting extensive physical damage.
There is also the new rule that has become part of NFPA 1851 for the selection and care of turnout gear mandating that any clothing older than 10 years from the date of manufacture be retired. Yet, what most departments struggle with are the more subtle circumstances where the evidence may not be so compelling. Thus, it would seem logical that if there was a tool that could make this determination easier, it should be embraced rather than discarded. Such is the case for a design feature called the liner access opening. A proposal has been made for the revision of NFPA 1971 that liner access openings should become mandatory for structural firefighting garments.
A liner access opening is a simple feature for being able to invert a garment liner and allow the inspection of interior layers. This feature is usually a designed opening in the garment where either a part of a seam can be opened or a slit has been installed in an accessible portion of the liner.
The port has to be wide enough for permitting an individual to reach in and pull the entire liner out through the opening, causing it to be turned inside out. In some cases, the port has a flap or it might have a closure consisting of snaps or hook and loop closure. The purpose of the flap or closure is to keep unintended objects out and prevent any accidental inversion of the liner. Most manufacturers put the liner access opening at bottom hem on coats and at the waist area of pants; however, there are other areas where it works equally well.
Examine interior
The purpose of a liner access opening is to be able to examine the interior of garment liners. Garment liners consist of the moisture barrier and the thermal barrier sewn together to form a two layer composite that is then attached to the outer shell through snaps, zippers, hook and loop tape, tabs, or a combination of these attachment means.
The liner does not have the features of the outer shell like heavy pockets, trim, and hardware, but can have simple pockets and often includes internal reinforcement layers at shoulders, elbows, and knees. The primary reason to want to inspect the liner interior is mainly because it is important to visually observe those parts of the moisture barrier and thermal barrier that are more susceptible to damage.
In the case of the moisture barrier, the film side for nearly all older moisture barriers is oriented towards the inside of the liner. It is on this side that the most moisture barrier seams are taped. Defects or damage to the film or loose tape that results in loss of garment liquid resistance cannot be readily seen by looking at the exterior of the liner.
Several years ago this was an issue when one particular moisture barrier film prematurely degraded by flaking and disintegrating into dust. It was only by carefully manipulating the liner that this problem could be detected. Similarly, the batting or nonwoven side of the thermal barrier is also oriented toward the liner interior.
This part of the thermal barrier is the lighter, loftier part. It has to be stabilized by being quilted to a more sturdy woven fabric. Some types of battings and nonwoven layers can migrate, resulting in loss of thermal insulation in that area.
Liner access openings have taken on new importance because of the requirement for a complete liner inspection that was established in the 2008 edition of NFPA 1851. Fire departments are required to conduct complete liner inspections annually starting three years after the date of the garment manufacture.
The complete liner inspection involves looking inside the liner to examine the interior conditions of the moisture barrier film side and batting/nonwoven side of the thermal barrier. The complete liner inspection also must include hydrostatic testing of six different locations on the moisture barrier side of the liner for water penetration resistance.
This inspection can only be conducted by opening the liner. If the liner does not have an access opening, then a portion of the garment seam must be removed and then the garment must be repaired by restitching and sealing the opened seam.
Simpler and quicker
Obviously, if a garment has a liner access opening, then the process of performing the complete liner inspection becomes much simpler and quicker. If the department uses an Independent Service Provider to conduct the complete liner inspection and the garment does not have a liner access opening, the inspection may be more costlier and potentially require the garment to be out of service longer for the inspection.
Simply put, the implementation of a liner access opening in garments is a logical requirement given that departments who properly care for and maintain their clothing are required to conduct annual complete liner inspections as set forth in NFPA 1851 (beginning three years after the manufacture date of the garment).
There are other circumstances where being able to examine the liner interior has significant merit. In cases where there are firefighter complaints about "leaky" garments or if the department has individuals that have been exposed to fires where damage is evident on the outside and want to see if the damage extends to the interior, the access opening offers an expedient means for making these assessments. A liner access opening also permits fire departments to check the quality of garment construction such as taping of moisture barrier seams and placement of reinforcement layers.
Opponents to the mandatory use of liner access openings argue that given the opening in the liner, firefighters will find ways to abuse garments and cause unnecessary damage to the garment. There have been specific claims that firefighters have stored items inside their liners or have written notes on the moisture barrier when an access opening has been present.
These claims are ridiculous and insulting to fire service. These problems are possible, but as with any gear, there is always the potential for some abuse and no standard can prevent all misuse of a product. Interestingly, some manufacturers already offer liner access openings as a standard feature at no cost to the firefighter.
So, why would individuals on a committee focused on improving firefighter safety be so opposed to the potential benefit of a simple design feature? Of course, committees operate best when there is ample input from those directly affected by proposed changes and this process is far from complete. As always, any new idea or proposal needs to gain full consideration and thoroughly examined before it is implemented to affect the entire fire service. Nevertheless, being able to look from the inside out for turnout gear appears to have more advantages than disadvantages and would not create new burdens for industry as most manufacturers already offer liner access openings.
Sponsored by GlobeJeffrey O. and Grace G. Stull are president and vice president respectively of International Personnel Protection, Inc., which provides expertise on the design, evaluation, selection and use of personnel protective clothing, equipment and related products to end users and manufacturers. They are considered amongst the leading experts in the field of personal protective equipment. Send questions or feedback to Jeff or Grace at Jeffrey.O.Stull@FireRescue1.com. The views of the author do not necessarily reflect those of the sponsor.
Balancing Breathability with Protection in Turnouts
PPE Update by Jeffrey O. and Grace G. Stull Sponsored by Globe |
Balancing breathability with protection in turnouts
Editor's note: In the following article, Jeffrey and Grace Stull outline how the stress impact of clothing on firefighters has been lessened in recent years. Now, as the NFPA begins a revision of the 1971 standard, consideration is being given to raising the breathability criteria to a higher level. Read on to learn the purpose of the total heat loss test, its consequences and the tradeoffs involved in design and share your views on proposed changes to the standard and own personal experiences in the member comments area below. |
By Jeffrey O. and Grace G. Stull
It has only been in the past 10 years when all garments were required to have a breathable moisture barrier. Prior to that time, most of the fire service wore protective coats and pants with impermeable coated barrier materials. In the late 1990s, the International Association of Fire Fighters fought endlessly to have the total heat loss test implemented as part of the NFPA 1971 standard for turnout gear and sponsored a major study that set the basis of the current requirement.
Presently, firefighters benefit from garments that are breathable. Breathability is a property of materials and composites, which permits the escape of moisture and the heat associated with that moisture from the interior of the garment to the outside environment. This property is considered important because in wearing heavy clothing such as turnout gear, the clothing traps heat that the body produces through metabolism and activity.
If left unchecked, the body core temperature can rise to dangerous levels and lead to the onset of heat stress. Heat stress can manifest itself in many different ways that include heat exhaustion, heat stroke, and ultimately death. The effects of heat stress may also include impairment of judgment and limit endurance. Given the extreme conditions of firefighting, it is no surprise that more than half the fatalities and a significant proportion of injuries to firefighters can be linked to stress-related causes.
The total heat loss (THL) test evaluates "clothing composites" (the layers of outer shell, moisture barrier, and thermal barrier) that are used in the construction of protective garments. Samples of the clothing composite are placed on a special hot plate that measures the energy for the plate to stay at a constant set point temperature (94 F).
The plate and the composite samples are located in a controlled environmental chamber at a lower temperature (77 F). The THL test is then performed in two different ways to measure the energy required to keep the plate at the set point temperature. In the first procedure, the testing is conducted dry.
Heat transfer
This way of testing evaluates the heat transfer from the skin to the outside environment that occurs through conduction, which is one of the major ways that the body dissipates heat. The second way attempts to simulate evaporate heat transfer (sweating), which is the other primary mode for how the body expels heat. In this part of the THL test, water is pumped through small holes in the hot plate (representing skin pores) to simulate sweating.
Heat loss occurs from the plate as the moisture moves through and exits the fabric system. The energies associated with both conductive and evaporative heat transfers are combined to estimate the total heat loss. This test result is reported in Watts per square meter of fabric composite materials. Higher total heat loss values indicate clothing systems that permit more heat to escape the garment and consequently result in less stress to the wearer.
The total heat loss test first appeared as a recommended turnout clothing evaluation method in the 1991 edition of NFPA 1971. At the time, the method was relegated to an appendix where, if desired, manufacturers could apply the THL test (or departments could specify the test) to characterize material breathability as an aspect of garment stress relief.
An attempt was made to make the test mandatory as part of the next revision of the standard (in 1997) but was blocked on administrative grounds in an appeal to the NFPA Standards Council.
The IAFF raised significant concerns about this decision, which provided the incentive to conduct comprehensive evaluation to show how garments having more breathable moisture barriers (with higher total heat loss values) could lessen the stress-related physiological effects of clothing on firefighters. This testing became known as the Indianapolis Field Study as it was conducted with the support of the Indianapolis Fire Department.
Significant reduction
The study showed a significant reduction in body core temperature for garments with higher total heat loss values and recommended a minimum requirement of 205 W/m2, citing the additional finding that a difference of 45 W/m2 was necessary to perceive a physiological impact for garment breathability. In comparison, most non-breathable material systems had total heat loss values in the range of 100 to 120 W/m2. Yet, the committee chose to conservatively set the new total heat loss requirement at 135 W/m2 based on the thinking that it was best to have the TPP test as a mandatory part of the standard with a lower limit to allow the industry to adjust their product offerings.
It was not until several years later that the total heat loss criterion was set at the 205 W/m2 recommended level scientifically demonstrated nine years earlier. The incorporation of the total heat loss test as part of the criteria for protective garments resulted in the elimination of impermeable moisture barrier materials.
Since higher total loss values mean less stress on firefighters, it would seem that total heat loss values should be set as high as possible. Yet there would be multiple tradeoffs created with this approach.
First, there are limits for the levels of total heat loss that can be achieved in firefighter protective clothing. All turnout gear must include a three layer material composite or at least clothing layers that provide the functional performance of the three layer system.
The principal function of the moisture barrier is to keep liquids out of the clothing interior. There is a narrow range of films that can accomplish this feature and still be breathable. Materials with very, very high breathability often cannot meet the liquid and bloodborne pathogen requirements of the NFPA 1971 standard.
Second, increasing total heat loss usually comes at the expense of decreased insulation against heat. It follows that keeping thermal energy from entering the clothing from the exterior environment is directly opposed to allowing body heat energy to escape from the clothing interior.
Thus it becomes a balancing act to select a material composite with relatively high total heat loss value without sacrificing thermal insulation (as measured by thermal protective performance or TPP). The criteria in NFPA 1971 for both total heat loss and TPP create a window of acceptable material systems.
Fewer systems
If the minimum total heat loss test requirement is raised significantly, it would mean that fewer material systems would be available for selection, some thermal barriers would be eliminated altogether, and that TPP values for composites would generally be lower with consequentially lower thermal insulation for protecting firefighters.
There are also limitations in the application of total heat loss testing. Just as TPP testing does not evaluate the entire garment for thermal insulation, total heat loss testing is a material test and does not evaluate the entire capability of the garment to dissipate heat. Areas of garments where there is trim, pockets, and reinforcements have lower or less breathability.
In contrast, these same areas of the garment have greater thermal insulation. The specification of garment design must account for which areas of the garment outside the three-layer composite need reinforcement and other materials and how these additional materials or components may contribute to stress.
While it is a worthy objective to increase the total heat loss criteria applied to firefighter protective garments, careful consideration must be given to weighing the advantages and disadvantages. Certainly, a higher total heat loss test can promote improvements in lessening the clothing and equipment imposed stress on firefighters. Yet, the total heat loss test is probably one of the few requirements in the NFPA 1971 that has been scientifically validated (through the IAFF Indianapolis Field Study).
Industry has become accustomed to balancing insulation and breathability needs. End user organizations are also recognizing that how other parts of the garments are designed also affect stress and that the total heat loss test does not address garment design, only material selection. Still, it is important for the NFPA committee to hear from the fire service as to their needs, issues, and what they consider to be a priority. We look forward to your comments below.
Jeffrey O. and Grace G. Stull are president and vice president respectively of International Personnel Protection, Inc., which provides expertise on the design, evaluation, selection and use of personnel protective clothing, equipment and related products to end users and manufacturers. International Personnel Protection, Inc. has conducted numerous studies for effectiveness and performance of protective clothing and equipment. Mr. and Mrs. Stull are currently members of several NFPA Technical Committees for Fire and Emergency Services Protective Clothing and Equipment and other groups for protective clothing and equipment. Both Mr. and Mrs. Stull participate in the government’s Interagency Board for Equipment Standardization and Interoperability. International Personnel Protection, Inc. is considered one of the leading sources of expertise in the field of personal protective equipment. Send questions or feedback to Jeff or Grace at Jeffrey.O.Stull@FireRescue1.com.
Check your PPE Between Calls
Understanding and using protective hoods
with Jeffrey O. and Grace G. Stull
Sponsored by Globe
Understanding and using protective hoods
By Jeffrey O. and Grace G. Stull
Of all the protective elements worn as part of the firefighter's ensemble, perhaps the least appreciated item is the protective hood. Over the past two decades, hoods have become a standard part of the ensemble.
The hood covers the exposed areas of the body that are not covered by the coat collar, SCBA facepiece or helmet. As such, the hood is considered to be an interface item somewhat like the wristlets of coats which help connect coat sleeves and gloves.
Interface areas are for the critical gaps in the ensemble where burns can readily occur if not properly protected. Therefore, the correct selection and use of the protective hood is essential for completing the envelope of protection in this critical head-neck interface area.
The majority of current hoods in the marketplace are of a sock configuration shaped much like a ski mask, having a face opening that fits over the SCBA facepiece. Hoods have bibs that extend down both sides and the front so that the hood remains tucked in under the collar of the coat.
NFPA 1971
The minimum lengths of the bibs are specified by NFPA 1971, Standard on Protective Ensembles for Structural and Proximity Fire Fighting. These lengths generally require the bibs to extend down a couple of inches below the neck on the front and the back and at a slightly shorter distance on the sides.
However, most hoods have longer bibs to ensure that the bib will stay inside the clothing. Some hoods have very broad hoods with panels that extend a significant distance down the shoulders and front and back. Consequently, there are a variety of different styles that are offered by different manufacturers with different bib configurations.
The hood face opening is elastic and likewise has to have minimum dimensions when evaluated according to NFPA 1971. The face opening must also demonstrate a certain size retention as the hood is repeatedly pulled over and taken off the firefighter's head.
Hoods with poor face opening designs can stretch out and are no longer able to make tight contact with the SCBA facepiece. While most knit materials tend to bounce back to their original dimensions after washing, in some cases the continued donning and doffing of the hood can result in elongated openings, which are ineffective.
Opening dimensions
The test in NFPA 1971 for retention of the face opening dimensions actually accounts for 50 repetitions of putting and taking the hood off of a manikin head.
There are relatively few other design features that are common to hoods. In years past, some manufacturers offered hoods with mesh materials in the area of the ear to facilitate the ability of firefighters to hear. There have also been hoods designed with mesh material at the crown of the hood directly underneath the protective helmet to provide for better air movement at the head.
However, there is some consideration of late that the hood should provide uniform insulation protection over the entire head. This issue is still being debated as the NFPA 1971 standard goes through its current revision process.
These products consist of one or two layers of a knit material. Common material fibers include Nomex, PBI, P84, Basofil, Flame Retardant Rayon (also called Viscose) or Carbon-based and various other flame-resistant fibers.
Some material layers are knit 100 percent of one fiber type while many are blends of two or more fibers. Some manufacturers configure their hoods with two layers of the same knit material, while other manufacturers offer one material layer on the outside and another for the inside against the wearer's skin.
Durability and performance
There are several differences in these materials for the department's or firefighter's consideration. They include the relative wearing comfort of the material, its overall durability, and of course its performance. Comfort and durability are best assessed by experience, particularly in talking with other departments that may be using a particular product.
Some products absorb moisture better than others or may feel better next to the skin. While hoods are considered a commodity-like product, subject to more frequent replacement compared with garments and other element ensembles, there is an expected service life that is mainly based on the anticipated level of use.
Most of the performance properties for hoods are the same evaluations that are applied to garment materials in NFPA 1971. This include flame resistance, heat resistance, thermal shrinkage resistance, burst strength, cleaning shrinkage resistance, seam strength, and thread melting resistance.
Some tests such as the flame resistance, burst strength, and seam strength are performed on small samples. Thermal shrinkage (shrinkage caused by high heat exposure) and cleaning shrinkage (shrinkage that results from laundering) are assessed on complete hoods.
The overall heat insulation effectiveness is determined through thermal protective performance (TPP) testing. In this test, hoods are only required to meet a value of 20, while garments have to offer a minimum value of 35 or higher.
The reason for this difference is because as an interface device, hoods do not have to provide as much protection since some attenuation of the heat is caused by the helmet ear covers, coat collar, and SCBA facepiece. Generally speaking, hoods offering the highest TPP values may be the heaviest or least comfortable; however, some novel materials provide very good insulation at low weights.
Unique designs
There are some unique hood designs which approximate multilayer garments by using normal garment outer shells combined with interior knit materials. Some of these designs have hoods that have a manual adjustment to permit closure around the SCBA facepice. In some rare cases, hoods are designed for integration with one specific type of SCBA.
While protective hoods are available in several designs throughout the industry, they are most often provided in only one size, though there are exceptions. Consequently, each firefighter has to be sure that the hood will comfortably fit and most importantly protect any uncovered area of the face not otherwise shielded by the one of the other ensemble elements.
This is best accomplished by putting the hood on and adjusting it as needed and then taking a look in a mirror. In particular, be sure that the hood is covering the sides of the SCBA facepiece and there are no gaps anywhere else in the face covering.
It is also important that your hood is positioned correctly as an interface element in the overall ensemble. For the hood to provide sufficient protection, the bib sections must be completely tucked underneath the coat with the collar in a raised position.
Ear flaps
The helmet ear flaps must also be fully deployed given that that the hood does not provide the same level of insulation as the rest of the garment. Most users will don their hood over their head with their head outside the face opening before putting on their coat (or right after putting on their coat) and then only deploy the hood when necessary at the fire scene. This practice works well only when the hood has been properly and fully positioned with the other ensemble elements before entering the fireground.
Proper care and maintenance is also critical to the hood. Each manufacturer should provide complete washing instructions. Given the simple design for hoods, the hoods are easily washed and dried for reuse.
Washing and drying procedures must be consistent with the manufacturer’s instructions to ensure long life and minimum protection. Similar practices must be exercised for correctly storing hoods out of sunlight and making sure they are dry before they are stored.
Hoods provide a valuable portion of the protection to the firefighter. In a 1990s study, the Fire Department of New York demonstrated the value of hood protective qualities in a variety of laboratory tests and showed how, together with department exposure statistics, proper hood use made the difference in reducing injuries to the head and faces of firefighters.
We look forward to any comments or questions you might have.
Sponsored by Globe
Jeffrey O. and Grace G. Stull are president and vice president respectively of International Personnel Protection, Inc., which provides expertise on the design, evaluation, selection and use of personnel protective clothing, equipment and related products to end users and manufacturers. They are considered amongst the leading experts in the field of personal protective equipment. Send questions or feedback to Jeff or Grace at Jeffrey.O.Stull@FireRescue1.com. The views of the author do not necessarily reflect those of the sponsor.
From PPE101.com