Blog Archive
-
▼
2010
(61)
-
►
June
(12)
- Defibtech DBP-2800 Battery Packs used in Lifeline ...
- Gear Down, Cool Down
- Always Check your SCBA
- Federal Ruling on High Visibility Vests
- Reactive Maintenance
- Preventive Maintenance Programs
- Predictive Maintenance Program
- Reliability Centered Maintenance Program
- How to Initiate Reliability Centered Maintenance
- Truck Company Operations - SCBA Donning Drill
- Truck Company Operations - SCBA Donning Drill #2
- SCBA Donning Drill
-
►
November
(29)
- Truck's Electrical System Was Source Of Fire At St...
- Firefighter Killed While Repairing Fire Truck
- UL Study on Firefighter Exposure to Smoke Particle...
- NIST Releases Study on Charleston (SC) Sofa Super ...
- Construction Concerns: Fall Protection Anchorages ...
- Personal Harness Use Poster
- Personal Harness Use
- HRT Bus Crashes Into Firetruck In Newport News
- Thermal Imager Use for First Responders
- More Thermal Imaging Information
- Thermal Imager Evaluation and Checklist
- SCBA Evolution Training
- MSA Firehawk M7 Advanced Firefighter Training
- MSA Firehawk M7 Training
- Woman Illegally Fired Over Facebook Remarks
- RAM Nozzle Article
- Siren Sounds: The Science Of Moving Vehicles Out O...
- Apparatus Requirements: Looking Ahead To 2020
- Brake Inspections Will Protect Lives
- What's Up With This Class A Foam? (Part 2 of 3)
- Class A Foam: The Smart Thing To Do (Part 3)
- Apparatus Requirements: Looking Ahead To 2020 (Par...
- Downhill Braking with Air Brakes
- General Information on Air Brakes
- Jake Brakes Explained
- Jake Brake Owner's Manual
- 10 Deadly Tanker Mistakes
- Firehouse Etiquette - Preparing for a shift
- Inside the San Francisco Fire Department Ladder Shop
-
►
June
(12)
Real Kings of Logistics
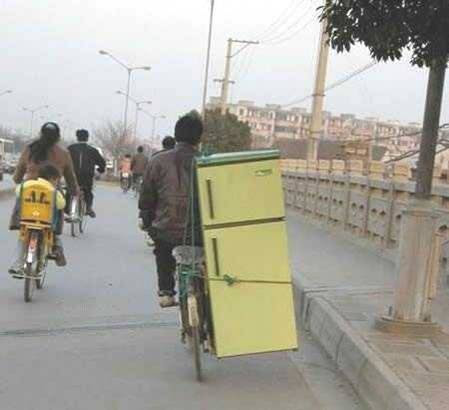
Wednesday, December 29, 2010
Firehouse Etiquette - Reporting for Duty
Do you know which station you are assigned to work in today? If you are regularly detailed, be sure that you are reporting to the correct station.
You should arrive early - 10 or 15 minutes early gives you time to exchange information with the person you are relieving. Earlier is better. You will find if you are known to relieve early, your relief will usually respect that and give you the same consideration.
What is the uniform of the day? Long sleeves or short? Any special events? If it is cold are you going to wear enhanced under clothing for warmth?
Anything else?
Tuesday, December 28, 2010
Nine People Charged in UK Terror Conspiracy: Homeland Defense & Terror News at Officer.com
Another reason to have situational awareness on calls. Who do you think will be there first? The fire department. What about secondary devices?
Dec. 27 Roundup: Pumper Rolls, New Deliveries, Santa’s Surprise
from FireTruckBlog.com
Eight Dead, Two Injured in New Orleans Fire. Warming Barrel Ignited Abandoned Warehouse
from Statter911.com
Deadliest fire in New Orleans in over 30 years.
Tuesday, November 16, 2010
Inside the San Francisco Fire Department Ladder Shop
Great video about SFFD's use of wooden ladders and why.
Monday, November 15, 2010
Firehouse Etiquette - Preparing for a shift
Preparing for a shift
What should you do the night before a shift?
Attitude - Think about what you are going to accomplish during your shift. You are there to run calls but there is more to it then that.
What about your physical training (PT)? Are you going to walk, run, lift weights, etc.?
What about your mental training? Fire/EMS journal review, read departmental orders, study for promotion, study OPM's.
What about practical training? Pulling hoselines, assembling a Thumper, SCBA drills.
Hygiene - Do you have all the supplies you need in your shower kit or station locker?
Nutrition - Are you bringing your meals to work or are you going to be in on meals with the rest of the shift and need money for groceries?
Family - Does your family know where you are working and how to get in touch with you other than your cell phone?
Overnight Items - Alarm clock, bedding, pillow, clothes for sleeping.
Any others?
Wednesday, November 10, 2010
10 Deadly Tanker Mistakes
This article discusses 10 deadly tanker mistakes that include:
1. Overloading the vehicle - This should not happen to our units because they are designed and built to carry water in the capacity specified.
2. Raising the center of gravity - Also, this should not be a problem with our tankers. They have been specifically designed for their function and none of the modification, if any, have changed the center of gravity.
3. Omitting tank baffles - All of our tanks have baffles. Ground Support also insures that the baffles are replaced when any tank work is being done.
4. Cutting and splicing the frame - Our vehicles are on chassis designed for the function. There should not be any notching or modifications to the frame. Even if a vehicle has a cracked frame that has been repaired, it will most likely not be permitted to respond under emergency conditions.
5. Not training drivers - This is an area that we have to be cautious. While the department require driver's training prior to being permitted to drive, there is not a specific tanker driver course. Given the differences in vehicle actions such as sloshing water and weight changes, the tanker driver should be someone with a lot of experience and training.
6. Not limiting vehicle speed - Based on NFPA 1901 our tankers top speeds should be 60 mile per hour. As you know, 60 mph is fast when you must make a quick turn or stop with a load of water. The driver must be aware of the vehicle's limitations and drive accordingly.
7. Not wearing seatbelts - WEAR YOUR SEATBELTS, enough said.
8. Not using a backing spotter - USE A SPOTTER. again enough said.
9. Not following NFPA 1901 - When specifying a vehicle, we make every effort to conform to the current edition of NFPA 1901. Any deviation is seriously considered.
10. Not performing regular maintenance - Our tankers are on the same maintenance schedule as our other apparatus. The driver is responsible for checking it at the beginning of the shift to insure that it is safe to operate.
Don't just think this applies to the tanker driver. It also applies to the pumper/tankers as well. Maybe more so. The drivers of pumper/tankers are driving the vehicle on more emergency runs and must heed these warnings to insure that they and their crew make it safely through their shift.
Jake Brake Owner's Manual
Downhill Braking with Air Brakes
This article describes snub braking which is the preferred method of downhill braking.
Snub Braking is:
1. Choose the proper gear for the road conditions.
2. Allow the truck to accelerate to the maximum safe speed.
3. Apply the brakes hard to reduce your speed by 5 mph.
4. Repeat until you reach the bottom of the hill.
Read the article for an explanation about why this works.
Tuesday, November 9, 2010
Class A Foam: The Smart Thing To Do (Part 3)
This article discusses the use of a brand of universal foam concentrate for multiple classes of fires.
What's Up With This Class A Foam? (Part 2 of 3)
(Click the link to go to the article)
This article describes the advantages of Class A foam.
Quick knock down.
Less water use.
Wetting agent.
Firefighter safety.
Do you think we should carry Class A foam ready for quick deployment?
RAM Nozzle Article
This article discusses the use of a RAM nozzle for quick knock down then advancing hand lines for final extinguishment. The hand lines can be advanced from the RAM by connecting a gated wye to the RAM. With this arrangement, one person can conduct the blitz and prepare the hand line awaiting the arrival of additional personnel.
What do you think?
Truck's Electrical System Was Source Of Fire At Station 3
A yet undetermined electrical problem with a fire vehicle caused over one million dollars damage. Let Ground Support know if you think you have a problem.
Friday, October 29, 2010
Draft NFPA Standard - Ambulance available for comment
October 29, 2010
NFPA Standards Council Approves Ambulance Draft
NFPA Standards Council has just approved release of a draft standard on automotive ambulances, NFPA 1917. Public proposals on this draft will be accepted until Dec. 15, 2010.
The draft document has the following scope and purpose:
1.1* Scope.
1.1.1 This standard establishes the minimum requirements for new automotive emergency medical services (EMS) ground vehicles used for out-of-hospital medical care and patient transport.
1.1.2 The term new as applied in this standard is intended to refer to the original construction of an ambulance using all new materials and parts.
1.2 Purpose. The purpose of this document is to specify minimum requirements, performance parameters, and essential criteria for the design of ground ambulances.
The technical committee on ambulances has addressed the following areas for design, construction and performance:
1. Chassis
2. Patient Compartment Area
3. Low Voltage and Line Voltage Electrical
4. Testing
The following links are provided to access and download the document:
The pre-ROP Draft has been posted on the NFPA 1917 doc info page under the Next Edition tab: http://www.nfpa.org/aboutthecodes/AboutTheCodes.asp?DocNum=1917
Tuesday, October 26, 2010
Pulse Oximeter Policy
BLS Ambulances - optional till 2012 then mandatory
BLS First Responders - optional
ALS Ambulance - required
ALS Chase and Engines - required
Policy Criteria
ALS Ambulances, Chase and Engines will meet our requirements if they are assigned a Lifepak with pulse ox capabilities.
ALS Ambulances, Chase and Engines are first priority if they do not have pulse oximeter capabilities.
BLS Ambulances are second priority and should have a pulse oximeter prior to January 1 2012.
BLS First Responders are a third priority and will be issued pulse oximeter if devices are available in our system.
ALS Ambulances, Chase and Engines may be issued a stand alone pulse oximeter as a backup if devices are available in our system.
Volunteer-purchased pulse oximeter will be maintained by us as long as it is cost effective to repair.
If a volunteer-purchased pulse oximeter is an optional item on the assigned unit, it will not be replaced by us if it is no longer supported by the manufacturer, if it is un-repairable or if devices are not available in our system.
It appears that the manufacturer will support the device for at least five years from the date of purchase.
The cost of our approved pulse oximeter is approximately $530.00. Use the following matrix to determine if a pulse oximeter is cost effective to repair.
Year of Service % of Original Cost Amount Allowed per Device
1st Year 70% $371
2nd Year 60% $318
3rd Year 50% $265
4th Year 40% $212
5th Year 30% $159
Since the manufacturer has a flat rate of $165.00, we may not be repairing devices that are over 4 years old.
Friday, October 22, 2010
Thursday, October 21, 2010
Wednesday, October 20, 2010
Tuesday, October 19, 2010
Thursday, September 30, 2010
Flash Flood Watch, Tornado Warning, Tornado Watch, Coastal Flooding
The current forecast is calling for 4 to 8 inches of rain total, with rain extending into the evening hours. The tornado watch is in effect, however sustained winds should not exceed 30 mph. High tides are predicted to be 2.5 feet above normal.
What to Do During a Tornado
If you are in: A structure (e.g. residence, small building, school, nursing home, hospital, factory, shopping center, high-rise building) : Go to a pre-designated shelter area such as a safe room, basement, storm cellar, or the lowest building level. If there is no basement, go to the center of an interior room on the lowest level (closet, interior hallway) away from corners, windows, doors, and outside walls. Put as many walls as possible between you and the outside. Get under a sturdy table and use your arms to protect your head and neck. Do not open windows.
If you are under a tornado WARNING, seek shelter immediately!
In a vehicle, trailer, or mobile home: Get out immediately and go to the lowest floor of a sturdy, nearby building or a storm shelter. Mobile homes, even if tied down, offer little protection from tornadoes
If you are outside with no shelter: Lie flat in a nearby ditch or depression and cover your head with your hands. Be aware of the potential for flooding.
Do not get under an overpass or bridge. You are safer in a low, flat location.
Never try to outrun a tornado in urban or congested areas in a car or truck. Instead, leave the vehicle immediately for safe shelter.
Watch out for flying debris. Flying debris from tornadoes causes most fatalities and injuries
Tuesday, September 28, 2010
New Links - Flu and Hurricane
Thursday, September 9, 2010
Emergency Response Boat 41 Commissioning
The boat is currently in-service and is a joint resource of the Fire and Police Departments.
Tuesday, September 7, 2010
Have a Water Supply Backup Plan
http://www.seattlepi.com/local/426252_FIRE07.html
Things to think about.
Do you know your pump well enough to manually correct potential problems?
Is the second engine in covering the first engine's hydrant and is it prepared to assume the attack engine position if necessary?
Do you have a secondary water source should the first fail?
What else do you think should be included in this list?
Thursday, September 2, 2010
Anne Arundel County Purchases Ladder Truck

Tuesday, August 24, 2010
Appliance Survey
APPLIANCE SURVEY
All “County Maintained” Stations (4, 5, 7, 8, 9, 10, 11, 18, 19, 21, 23, 26, 27, 29, 30, 31, 32,
33, 40 & 41) are directed to provide the following information on station appliances:
Make:
Model #:
Serial #:
County Bar Code #:
Approximate Age:
Appliances that we require the information on are dishwashers, washing machines, dryers, stove,
refrigerators and free-standing ice machines.
If an appliance does not have a County Bar Code, please note that as well.
Please forward the information for each appliance in the station to “fdfms” via Groupwise.
Please complete the survey and have the information submitted by September 3, 2010, “B”
shift.
If you have any questions, please contact Lisa Scholz on ext. 8330.
Monday, July 26, 2010
Field Testing of Wheel Chocks Manufactured with Recycled Plastic
SCBA HUDS
Any questions may be directed to any of the Air Shop personnel or Ground Support 5.
AMBULANCE ELECTRICAL SYSTEMS
1. Shoreline connected to vehicle.
2. Master switch in the “off” position.
3. Module disconnect switch in the “off” position.
The shoreline energizes the 110v electrical outlets in the vehicle as well as the vehicle battery conditioner. When vehicle components are left energized while the vehicle is on shore power, the power is taken from the vehicle batteries which must be replaced by the conditioner. This puts unnecessary strain on the batteries and depending on the drain on the battery, the conditioner may not be able to keep the battery in a fully charged state. Items which need recharging such as cell phones, computers, etc. can be plugged into the 100v outlets and receive power for charging without affecting the vehicle’s electrical system.
Any questions may be directed to any of the Ground Support personnel.
Sunday, July 25, 2010
Balancing Footware Function with Protection
|
Balancing footwear function with protection
By Jeffrey O. and Grace G. Stull
In our previous article, we addressed issues related to gloves and how tradeoffs exist between performance and functionality. In this column, we examine the same concerns for firefighter footwear. Generally, there are fewer issues for footwear than there are for gloves, primarily because it is easier to achieve more robust protection of the feet compared to the hands (it is not necessary to insulate each toe the way each finger must be insulated for gloves). Nevertheless, there are still aspects of footwear use that must be considered, not all of which are addressed in NFPA 1971, the standard that covers protective footwear for structural firefighting.
Performance requirements
Currently, a number of performance requirements are applied to firefighter footwear in NFPA 1971. Whole footwear is tested for heat resistance, flame resistance, overall liquid integrity, and electrical insulation.
Footwear seams are evaluated for liquid penetration resistance (against fireground chemicals like battery acid, gasoline, and hydraulic fluid) and viral penetration resistance (for assessing leakage of blood and body fluids that may be contaminated with pathogenic organisms such as Hepatitis).
The upper portion of the footwear is tested for radiant heat resistance, conductive heat resistance, cut resistance, and puncture resistance.
The toe section is evaluated for impact and compression resistance.
Footwear soles are tested for puncture resistance, abrasion resistance, conductive heat resistance, and slip resistance or traction (the puncture and heat conduction tests are different than those applied to the footwear upper).
The shank (a metal or composite piece providing stiffness between the front of the heel and the back of the forefoot in the sole) is tested for bending resistance.
Hardware is tested for corrosion resistance, and eyelets and stud hooks, if present, are tested for detachment strength.
Thread is tested for melting temperature.
Footwear labels are evaluated for legibility and durability.
Design requirements
There are also several design requirements for firefighter footwear. Footwear must have a sole with a heel, an upper with a lining, an insole with a puncture resistance device (a metal plate or composite layer set above the outer sole) and a permanently integrated impact and compression resistant toe cap (may be metal or composite). As of the last edition, the footwear must be at least 10 inches high as measured from the inside of the footwear with the insole in place to the highest point on the boot where there is continuous liquid protection.
NFPA also specifies that a certain range of heel breast angle be used (this is the interior angle formed between the heel and the sole), that no hardware penetrate from the outside of the footwear to the lining (to act as an avenue for heat conduction or liquid leakage), and that nails or screws must not be used for attaching the sole to the boots.
Lastly, NFPA 1971 requires that manufacturers make available an extensive set of footwear sizing with unique sizes for men and women including half sizes and a minimum of three widths over the range of sizes 5 to 13 for men and sizes 5 to 10 for women. This sizing design requirement is the most extensive footwear requirement outside of the military for work-based footwear.
Range of options
It is well established that the firefighting protective ensemble takes a variety of forms with each of the available products offering different advantages and disadvantages. Even with the design requirements, manufacturers have the latitude to pursue different designs and choices of materials. Conventionally, there are rubber boots and leather boots. There are also some boots that combine different materials such as leather and durable fabrics.
There are a number of different lining materials, barrier materials, closure options, and methods of construction. All of these attributes provide the fire service with a multitude of choices for footwear that conform to the NFPA 1971 standard; but this does not mean that all types of footwear protect firefighters to the same level or even offer the same levels of functional use. Further, there are different preferences for footwear by individual firefighters with some aspects of NFPA 1971-based performance being addressed well, some not so well and others not at all.
Generally, there are no complaints about the levels of insulation provided by footwear, which in turn are affected by the tests in the standard that set minimum protection requirements. While a slip resistance is applied to footwear as part of NFPA 1971, there are concerns that the test and criteria do not do what they are supposed to do — ensure appropriate levels of traction for firefighters on slick surfaces.
Consequently, some work is ongoing by the responsible committee to identify a more suitable test that better ranks footwear for its traction consistent with field observations. As an example of footwear attributes where there are no requirements, nothing in the current standard addresses the functional performance of footwear as is done for gloves (such as dexterity and grip testing).
Footwear performance
Functional footwear performance is a legitimate concern for firefighters. Footwear must not only protect well against different fireground hazards (heat, flame, electrical shock, liquids, pathogens, and the physical environment), but it must permit firefighters to be active with appropriate levels of agility and comfort.
Footwear that does not fit well or is not comfortable will create problems. Many firefighters do not wear their footwear continuously over long periods of time, but some responses may require wearing footwear for an extended duration. It goes without saying that footwear should not chaff firefighters' feet or legs and should not cause blisters. This is one of the reasons why NFPA dictates a diverse range of sized footwear be provided to the fire service. But like regular shoes, various firefighter footwear products fit individual firefighters differently.
An important aspect in the fit of footwear is ankle support. Good ankle support helps to alleviate potential injuries caused by stepping on uneven or sloping surfaces, activities that are a routine part of firefighting (stains and sprains remain the highest proportion of all firefighter lost time injuries). Different footwear types provide different degrees of ankle support based on the inherent design of the footwear and its ability to properly fit the firefighter. Yet, prescribing ankle support in footwear is not easily done.
Footwear weight is another factor. As expected, heavier footwear will put a strain on the wearer, potentially leading to earlier fatigue and changing the gait of firefighters as some recent studies have suggested. Still, the specification of weight alone cannot address this issue as there are several factors that can affect footwear imposed stress and firefighter agility. For example, the flexibility of the materials, the actual footwear height, traction as imparted by the outer sole and tread design, and individual firefighter coordination can all have a bearing on this aspect of functional performance.
Finding the right fit
Short of each fire department field testing footwear choices, one way to address functional footwear performance that captures some of the factors affecting footwear performance may be through a repeatable laboratory test. A proposal has been put forward to create an "agility test" for footwear in a manner similar to the "dexterity test" that attempts to capture functional aspects of glove design and performance. The test involves test subjects wearing firefighter footwear and running an agility course. The times for completing the course are compared with the times that the same subjects gain on the course while wearing running shoes. Larger percentage differences in the times mean that the firefighter footwear being tested causes a loss of normal agility that would be provided with a well-fitted, lightweight athletic shoe. Thus, in comparing one type of firefighter footwear with another type, the footwear exhibiting the higher percentage change would be considered to having the least desirable impact on firefighter agility.
While this test approach in no shape or form represents fireground activity, nor is intended to, it is an attempt to find a repeatable and controllable means to discriminate footwear design issues that contribute to firefighter agility consistent with the experience of firefighters. Preliminary attempts at using this test have shown that the test ranks footwear consistent with how firefighters perceive differences in different product agility and functional performance on the fireground. These results further show measured differences between products to be significant. If further proven out, this test as a possible requirement in the NFPA 1971 standard could become a tool when combined with practical aspects of footwear performance that helps manufacturers improve footwear design towards more form fitting, comfortable, and functional boots.
No test can replace direct assessments of the product under the conditions of actual use. Fire departments and firefighters should judge for themselves which products provide the right combination of performance and functional use. Nevertheless, the requirements in NFPA 1971 are intended to set the minimum requirements for footwear that guarantee baseline protection and functionality. By setting minimum requirements in NFPA 1971, fire departments and individual firefighters are then free to choose the products best meeting their needs. Moreover, it helps those organizations that simply don't have the resources or ability to run their own evaluations. An attempt to address functionality as part of footwear requirements in NFPA 1971 will help in this regard as it provides a consistent measurement technique to help assess footwear impact on individual firefighters.
In closing, we want to thank our readership for their thoughtful comments and insight. We do appreciate your continued interest and suggestions on the many issues we raise in our column.
Sponsored by GlobeJeffrey O. and Grace G. Stull are president and vice president respectively of International Personnel Protection, Inc., which provides expertise on the design, evaluation, selection and use of personnel protective clothing, equipment and related products to end users and manufacturers. They are considered amongst the leading experts in the field of personal protective equipment. Send questions or feedback to Jeff or Grace at Jeffrey.O.Stull@FireRescue1.com. The views of the author do not necessarily reflect those of the sponsor.
Friday, June 18, 2010
Monday, June 14, 2010
How to Initiate Reliability Centered Maintenance
1. Develop a Master equipment list identifying the equipment in your facility.
2. Prioritize the listed components based on importance to process.
3. Assign components into logical groupings.
4. Determine the type and number of maintenance activities required and periodicity using:
a. Manufacturer technical manuals
b. Machinery history
c. Root cause analysis findings - Why did it fail?
d. Good engineering judgment
5. Assess the size of maintenance staff.
6. Identify tasks that may be performed by operations maintenance personnel.
7. Analyze equipment failure modes and effects.
8. Identify effective maintenance tasks or mitigation strategies.
From Operations & Maintenance Best Practices - A Guide to Operational Efficiency July 2004
Reliability Centered Maintenance Program
Reliability centered maintenance (RCM) magazine provides the following definition of RCM: “a process used to determine the maintenance requirements of any physical asset in its operating context.” Basically, RCM methodology deals with some key issues not dealt with by other maintenance programs. It recognizes that all equipment in a facility is not of equal importance to either the process or facility safety. It recognizes that equipment design and operation differs and that different equipment will have a higher probability to undergo failures from different degradation mechanisms than others.
It also approaches the structuring of a maintenance program recognizing that a facility does not have unlimited financial and personnel resources and that the use of both need to be prioritized and optimized. In a nutshell, RCM is a systematic approach to evaluate a facility’s equipment and resources to best mate the two and result in a high degree of facility reliability and cost-effectiveness.
RCM is highly reliant on predictive maintenance but also recognizes that maintenance activities on equipment that is inexpensive and unimportant to facility reliability may best be left to a reactive maintenance approach.
The following maintenance program breakdowns of continually top-performing facilities would echo the RCM approach to utilize all available maintenance approaches with the predominant methodology being predictive.
• <10% Reactive
• 25% to 35% Preventive
• 45% to 55% Predictive.
Because RCM is so heavily weighted in utilization of predictive maintenance technologies, its program advantages and disadvantages mirror those of predictive maintenance. In addition to these advantages, RCM will allow a facility to more closely match resources to needs while improving reliability and decreasing cost.
Advantages
• Can be the most efficient maintenance program.
• Lower costs by eliminating unnecessary maintenance or overhauls.
• Minimize frequency of overhauls.
• Reduced probability of sudden equipment failures.
• Able to focus maintenance activities on critical components.
• Increased component reliability.
• Incorporates root cause analysis.
Disadvantages
• Can have significant startup cost, training, equipment, etc.
• Savings potential not readily seen by management.
From Operations & Maintenance Best Practices - A Guide to Operational Efficiency July 2004
Predictive Maintenance Program
Predictive maintenance can be defined as follows: Measurements that detect the onset of a degradation mechanism, thereby allowing causal stressors to be eliminated or controlled prior to any significant deterioration in the component physical state. Results indicate current and future functional capability.
Basically, predictive maintenance differs from preventive maintenance by basing maintenance need on the actual condition of the machine rather than on some preset schedule. You will recall that preventive maintenance is time-based. Activities such as changing lubricant are based on time, like calendar time or equipment run time. For example, most people change the oil in their vehicles every 3,000 to 5,000 miles traveled. This is effectively basing the oil change needs on equipment run time. No concern is given to the actual condition and performance capability of the oil. It is changed because it is time.
This methodology would be analogous to a preventive maintenance task. If, on the other hand, the operator of the car discounted the vehicle run time and had the oil analyzed at some periodicity to determine its actual condition and lubrication properties, he/she may be able to extend the oil change until the vehicle had traveled 10,000 miles. This is the fundamental difference between predictive maintenance and preventive maintenance, whereby predictive maintenance is used to define needed maintenance task based on quantified material/equipment condition.
The advantages of predictive maintenance are many. A well-orchestrated predictive maintenance program will all but eliminate catastrophic equipment failures. We will be able to schedule maintenance activities to minimize or delete overtime cost. We will be able to minimize inventory and order parts, as required, well ahead of time to support the downstream maintenance needs.
We can optimize the operation of the equipment, saving energy cost and increasing plant reliability. Past studies have estimated that a properly functioning predictive maintenance program can provide a savings of 8% to 12% over a program utilizing preventive maintenance alone. Depending on a facility’s reliance on reactive maintenance and material condition, it could easily recognize savings opportunities exceeding 30% to 40%.
In fact, independent surveys indicate the following industrial average savings resultant from initiation of a functional predictive maintenance program:
• Return on investment: 10 times
• Reduction in maintenance costs: 25% to 30%
• Elimination of breakdowns: 70% to 75%
• Reduction in downtime: 35% to 45%
• Increase in production: 20% to 25%.
On the down side, to initially start into the predictive maintenance world is not inexpensive. Much of the equipment requires cost in excess of $50,000. Training of in-plant personnel to effectively utilize predictive maintenance technologies will require considerable funding. Program development will require an understanding of predictive maintenance and a firm commitment to make the program work by all facility organizations and management.
Advantages
• Increased component operational life/availability.
• Allows for preemptive corrective actions.
• Decrease in equipment or process downtime.
• Decrease in costs for parts and labor.
• Better product quality.
• Improved worker and environmental safety.
• Improved worker moral.
• Energy savings.
• Estimated 8% to 12% cost savings over preventive maintenance program.
Disadvantages
• Increased investment in diagnostic equipment.
• Increased investment in staff training.
• Savings potential not readily seen by management.
From Operations & Maintenance Best Practices - A Guide to Operational Efficiency July 2004
Preventive Maintenance Programs
Preventive maintenance can be defined as follows: Actions performed on a time- or machine-run-based schedule that detect, preclude, or mitigate degradation of a component or system with the aim of sustaining or extending its useful life through controlling degradation to an acceptable level. The U.S. Navy pioneered preventive maintenance as a means to increase the reliability of their vessels. By simply expending the necessary resources to conduct maintenance activities intended by the equipment designer, equipment life is extended and its reliability is increased.
In addition to an increase in reliability, dollars are saved over that of a program just using reactive maintenance. Studies indicate that this savings can amount to as much as 12% to 18% on the average. Depending on the facilities current maintenance practices, present equipment reliability, and facility downtime, there is little doubt that many facilities purely reliant on reactive maintenance could save much more than 18% by instituting a proper preventive maintenance program.
While preventive maintenance is not the optimum maintenance program, it does have several advantages over that of a purely reactive program. By performing the preventive maintenance as the equipment designer envisioned, we will extend the life of the equipment closer to design. This translates into dollar savings. Preventive maintenance (lubrication, filter change, etc.) will generally run the equipment more efficiently resulting in dollar savings.
While we will not prevent equipment catastrophic failures, we will decrease the number of failures. Minimizing failures translate into maintenance and capitol cost savings.
Advantages
• Cost effective in many capital-intensive processes.
• Flexibility allows for the adjustment of maintenance periodicity.
• Increased component life cycle.
• Energy savings.
• Reduced equipment or process failure.
• Estimated 12% to 18% cost savings over reactive maintenance program.
Disadvantages
• Catastrophic failures still likely to occur.
• Labor intensive.
• Includes performance of unneeded maintenance.
• Potential for incidental damage to components in conducting unneeded maintenance.
From Operations & Maintenance Best Practices - A Guide to Operational Efficiency July 2004
Reactive Maintenance
The first program is a reactive maintenance program. Reactive maintenance is basically the “run it till it breaks” maintenance mode. No actions or efforts are taken to maintain the equipment as the designer originally intended to ensure design life is reached. Studies as recent as the winter of 2000 indicate this is still the predominant mode of maintenance in the United States. The referenced study breaks down the average maintenance program as follows:
• >55% Reactive
• 31% Preventive
• 12% Predictive
• 2% Other.
Note that more than 55% of maintenance resources and activities of an average facility are still reactive. Advantages to reactive maintenance can be viewed as a double-edged sword. If we are dealing with new equipment, we can expect minimal incidents of failure. If our maintenance program is purely reactive, we will not expend manpower dollars or incur capitol cost until something breaks. Since we do not see any associated maintenance cost, we could view this period as saving money.
The downside is reality. In reality, during the time we believe we are saving maintenance and capital cost, we are really spending more dollars than we would have under a different maintenance approach. We are spending more dollars associated with capital cost because, while waiting for the equipment to break, we are shortening the life of the equipment resulting in more frequent replacement. We may incur cost upon failure of the primary device associated with its failure causing the failure of a secondary device. This is an increased cost we would not have experienced if our maintenance program was more proactive.
Our labor cost associated with repair will probably be higher than normal because the failure will most likely require more extensive repairs than would have been required if the piece of equipment had not been run to failure. Chances are the piece of equipment will fail during off hours or close to the end of the normal workday. If it is a critical piece of equipment that needs to be back on-line quickly, we will have to pay maintenance overtime cost. Since we expect to run equipment to failure, we will require a large material inventory of repair parts. This is a cost we could minimize under a different maintenance strategy.
Advantages
• Low cost.
• Less staff.
Disadvantages
• Increased cost due to unplanned downtime of equipment.
• Increased labor cost, especially if overtime is needed.
• Cost involved with repair or replacement of equipment.
• Possible secondary equipment or process damage from equipment failure.
• Inefficient use of staff resources.
From Operations & Maintenance Best Practices - A Guide to Operational Efficiency July 2004
Federal Ruling on High Visibility Vests
FireRescue1 Staff
A much-anticipated and wide-reaching change aimed at first responder safety takes effect Monday. The Federal Highway Administration's Worker Visibility Rule (23CFR 634) now requires anyone — including firefighters, emergency medical workers and police — working on federal highways to wear vests that meet ANSI standards for high-visibility. But it also includes a change that exempts firefighters who are near flame, heat or hazardous materials.
Firefighters working on roadways outside the 'hot zone' are required to wear high-visibility vests. An exception to the rule The rule has stirred controversy in the fire service, primarily because most high-visibility vests are not flame resistant to NFPA standards. The interim rule exempting the fire service, announced by the FHWA on Friday, is in response to concerns voiced by the fire service. "The FHWA had received numerous comments from firefighters expressing safety concerns about the vests," according to Hari Kalla, team leader in the FHWA Office of Transportation Operations, which manages the updating and publishing of traffic rules. The FHWA has worked with departments and national fire service organizations to publicize the rule, which was published in 2006, and give those affected a chance to comment. "Based on the number of calls we have gotten, we think it's very well publicized," said Kalla, adding, "We're hoping to be able to continue to help people if they have questions or concerns."
Departments that buck the new rule may see financial repercussions. The FHWA has the authority to withhold funding from states that are found to be non-compliant with FHWA rules. Should a collision involving a firefighter occur, compliance also limits the risk of legal liability for departments. Kalla is quick to stress that the objective of the rule is not to penalize departments. "Most importantly, it's for worker safety," said Kalla.
Apparel Available
Apparel manufacturers have been quick to respond to the new rule, with Lion Apparel last weekend introducing the first flame resistant vest that meets the visibility standards set out by the FHWA. "If you do get into a hot situation, it's not going to melt like a lot of the vests," said Nick Curtis, vice president of global product development at Lion. He also said that many orders for the new vests had been cancelled following the FHWA's announcement of the exception for firefighters. The vest, which can be worn over turnout gear, is designed for firefighters with pockets and a break-away system for easy doffing and rehab. The company hopes it will provide a versatile option for firefighters working on roadways, despite the changed rule, according to Curtis. "If there's an extended incident where visibility is required but turnouts aren't because there's not a known assessed risk of fire, then the vest could be worn without turnout," Curtis said. "The reason to have it be flame resistant is that anything could happen."
From PPE101.com
Always Check your SCBA
You should always regularly check your own SCBA, so you can be safe in the knowledge that it’s going to work properly when you need it. Make sure you check the whole SCBA, especially the cylinder to ensure that it is full to maximize your operating time. A cylinder not full to the max with air means less operational time.
Make sure that all the straps, including the straps on your face piece, are correctly adjusted to suit your needs. And, open the cylinder valve fully whenever turning the mask on. Not having the cylinder fully opened can result in a sudden loss of air when operating.
From PPE101.com
Gear Down, Cool Down
From PPE101.com
Defibtech DBP-2800 Battery Packs used in Lifeline AED and ReviveR AED: Recall
http://www.fda.gov/Safety/MedWatch/SafetyInformation/SafetyAlertsforHumanMedicalProducts/ucm214916.htm