This is the third in a series of post describing the various types of maintenance programs that are used for equipment, vehicles, and facilities. The third program is a predictive maintenance program.
Predictive maintenance can be defined as follows: Measurements that detect the onset of a degradation mechanism, thereby allowing causal stressors to be eliminated or controlled prior to any significant deterioration in the component physical state. Results indicate current and future functional capability.
Basically, predictive maintenance differs from preventive maintenance by basing maintenance need on the actual condition of the machine rather than on some preset schedule. You will recall that preventive maintenance is time-based. Activities such as changing lubricant are based on time, like calendar time or equipment run time. For example, most people change the oil in their vehicles every 3,000 to 5,000 miles traveled. This is effectively basing the oil change needs on equipment run time. No concern is given to the actual condition and performance capability of the oil. It is changed because it is time.
This methodology would be analogous to a preventive maintenance task. If, on the other hand, the operator of the car discounted the vehicle run time and had the oil analyzed at some periodicity to determine its actual condition and lubrication properties, he/she may be able to extend the oil change until the vehicle had traveled 10,000 miles. This is the fundamental difference between predictive maintenance and preventive maintenance, whereby predictive maintenance is used to define needed maintenance task based on quantified material/equipment condition.
The advantages of predictive maintenance are many. A well-orchestrated predictive maintenance program will all but eliminate catastrophic equipment failures. We will be able to schedule maintenance activities to minimize or delete overtime cost. We will be able to minimize inventory and order parts, as required, well ahead of time to support the downstream maintenance needs.
We can optimize the operation of the equipment, saving energy cost and increasing plant reliability. Past studies have estimated that a properly functioning predictive maintenance program can provide a savings of 8% to 12% over a program utilizing preventive maintenance alone. Depending on a facility’s reliance on reactive maintenance and material condition, it could easily recognize savings opportunities exceeding 30% to 40%.
In fact, independent surveys indicate the following industrial average savings resultant from initiation of a functional predictive maintenance program:
• Return on investment: 10 times
• Reduction in maintenance costs: 25% to 30%
• Elimination of breakdowns: 70% to 75%
• Reduction in downtime: 35% to 45%
• Increase in production: 20% to 25%.
On the down side, to initially start into the predictive maintenance world is not inexpensive. Much of the equipment requires cost in excess of $50,000. Training of in-plant personnel to effectively utilize predictive maintenance technologies will require considerable funding. Program development will require an understanding of predictive maintenance and a firm commitment to make the program work by all facility organizations and management.
Advantages
• Increased component operational life/availability.
• Allows for preemptive corrective actions.
• Decrease in equipment or process downtime.
• Decrease in costs for parts and labor.
• Better product quality.
• Improved worker and environmental safety.
• Improved worker moral.
• Energy savings.
• Estimated 8% to 12% cost savings over preventive maintenance program.
Disadvantages
• Increased investment in diagnostic equipment.
• Increased investment in staff training.
• Savings potential not readily seen by management.
From Operations & Maintenance Best Practices - A Guide to Operational Efficiency July 2004
Blog Archive
-
▼
2010
(61)
-
▼
June
(12)
- Defibtech DBP-2800 Battery Packs used in Lifeline ...
- Gear Down, Cool Down
- Always Check your SCBA
- Federal Ruling on High Visibility Vests
- Reactive Maintenance
- Preventive Maintenance Programs
- Predictive Maintenance Program
- Reliability Centered Maintenance Program
- How to Initiate Reliability Centered Maintenance
- Truck Company Operations - SCBA Donning Drill
- Truck Company Operations - SCBA Donning Drill #2
- SCBA Donning Drill
-
▼
June
(12)
Real Kings of Logistics
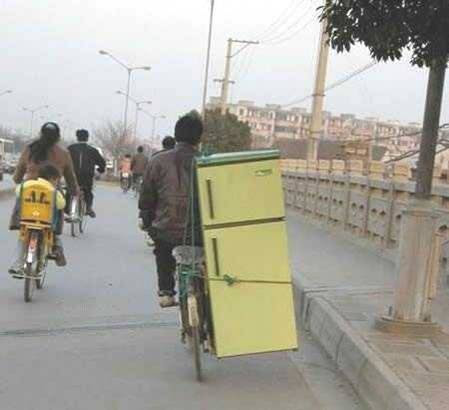
Monday, June 14, 2010
Subscribe to:
Post Comments (Atom)
No comments:
Post a Comment