This is the first in a series of post describing the various types of maintenance programs that are used for equipment, vehicles, and facilities.
The first program is a reactive maintenance program. Reactive maintenance is basically the “run it till it breaks” maintenance mode. No actions or efforts are taken to maintain the equipment as the designer originally intended to ensure design life is reached. Studies as recent as the winter of 2000 indicate this is still the predominant mode of maintenance in the United States. The referenced study breaks down the average maintenance program as follows:
• >55% Reactive
• 31% Preventive
• 12% Predictive
• 2% Other.
Note that more than 55% of maintenance resources and activities of an average facility are still reactive. Advantages to reactive maintenance can be viewed as a double-edged sword. If we are dealing with new equipment, we can expect minimal incidents of failure. If our maintenance program is purely reactive, we will not expend manpower dollars or incur capitol cost until something breaks. Since we do not see any associated maintenance cost, we could view this period as saving money.
The downside is reality. In reality, during the time we believe we are saving maintenance and capital cost, we are really spending more dollars than we would have under a different maintenance approach. We are spending more dollars associated with capital cost because, while waiting for the equipment to break, we are shortening the life of the equipment resulting in more frequent replacement. We may incur cost upon failure of the primary device associated with its failure causing the failure of a secondary device. This is an increased cost we would not have experienced if our maintenance program was more proactive.
Our labor cost associated with repair will probably be higher than normal because the failure will most likely require more extensive repairs than would have been required if the piece of equipment had not been run to failure. Chances are the piece of equipment will fail during off hours or close to the end of the normal workday. If it is a critical piece of equipment that needs to be back on-line quickly, we will have to pay maintenance overtime cost. Since we expect to run equipment to failure, we will require a large material inventory of repair parts. This is a cost we could minimize under a different maintenance strategy.
Advantages
• Low cost.
• Less staff.
Disadvantages
• Increased cost due to unplanned downtime of equipment.
• Increased labor cost, especially if overtime is needed.
• Cost involved with repair or replacement of equipment.
• Possible secondary equipment or process damage from equipment failure.
• Inefficient use of staff resources.
From Operations & Maintenance Best Practices - A Guide to Operational Efficiency July 2004
Blog Archive
-
▼
2010
(61)
-
▼
June
(12)
- Defibtech DBP-2800 Battery Packs used in Lifeline ...
- Gear Down, Cool Down
- Always Check your SCBA
- Federal Ruling on High Visibility Vests
- Reactive Maintenance
- Preventive Maintenance Programs
- Predictive Maintenance Program
- Reliability Centered Maintenance Program
- How to Initiate Reliability Centered Maintenance
- Truck Company Operations - SCBA Donning Drill
- Truck Company Operations - SCBA Donning Drill #2
- SCBA Donning Drill
-
▼
June
(12)
Real Kings of Logistics
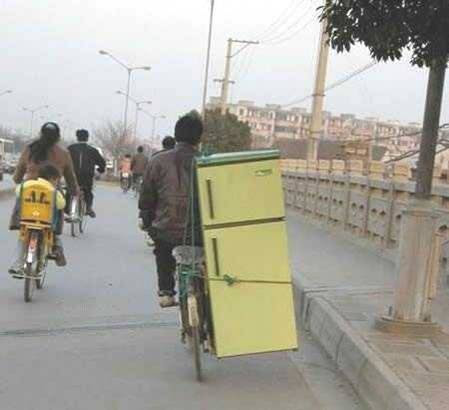
Monday, June 14, 2010
Subscribe to:
Post Comments (Atom)
No comments:
Post a Comment