This is the fourth in a series of post describing the various types of maintenance programs that are used for equipment, vehicles, and facilities. The fourth program is a reliability centered maintenance program.
Reliability centered maintenance (RCM) magazine provides the following definition of RCM: “a process used to determine the maintenance requirements of any physical asset in its operating context.” Basically, RCM methodology deals with some key issues not dealt with by other maintenance programs. It recognizes that all equipment in a facility is not of equal importance to either the process or facility safety. It recognizes that equipment design and operation differs and that different equipment will have a higher probability to undergo failures from different degradation mechanisms than others.
It also approaches the structuring of a maintenance program recognizing that a facility does not have unlimited financial and personnel resources and that the use of both need to be prioritized and optimized. In a nutshell, RCM is a systematic approach to evaluate a facility’s equipment and resources to best mate the two and result in a high degree of facility reliability and cost-effectiveness.
RCM is highly reliant on predictive maintenance but also recognizes that maintenance activities on equipment that is inexpensive and unimportant to facility reliability may best be left to a reactive maintenance approach.
The following maintenance program breakdowns of continually top-performing facilities would echo the RCM approach to utilize all available maintenance approaches with the predominant methodology being predictive.
• <10% Reactive
• 25% to 35% Preventive
• 45% to 55% Predictive.
Because RCM is so heavily weighted in utilization of predictive maintenance technologies, its program advantages and disadvantages mirror those of predictive maintenance. In addition to these advantages, RCM will allow a facility to more closely match resources to needs while improving reliability and decreasing cost.
Advantages
• Can be the most efficient maintenance program.
• Lower costs by eliminating unnecessary maintenance or overhauls.
• Minimize frequency of overhauls.
• Reduced probability of sudden equipment failures.
• Able to focus maintenance activities on critical components.
• Increased component reliability.
• Incorporates root cause analysis.
Disadvantages
• Can have significant startup cost, training, equipment, etc.
• Savings potential not readily seen by management.
From Operations & Maintenance Best Practices - A Guide to Operational Efficiency July 2004
Blog Archive
-
▼
2010
(61)
-
▼
June
(12)
- Defibtech DBP-2800 Battery Packs used in Lifeline ...
- Gear Down, Cool Down
- Always Check your SCBA
- Federal Ruling on High Visibility Vests
- Reactive Maintenance
- Preventive Maintenance Programs
- Predictive Maintenance Program
- Reliability Centered Maintenance Program
- How to Initiate Reliability Centered Maintenance
- Truck Company Operations - SCBA Donning Drill
- Truck Company Operations - SCBA Donning Drill #2
- SCBA Donning Drill
-
▼
June
(12)
Real Kings of Logistics
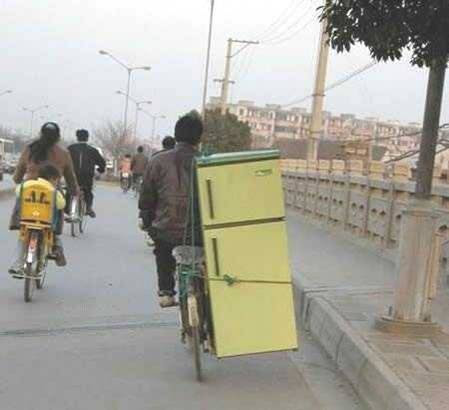
Monday, June 14, 2010
Subscribe to:
Post Comments (Atom)
No comments:
Post a Comment